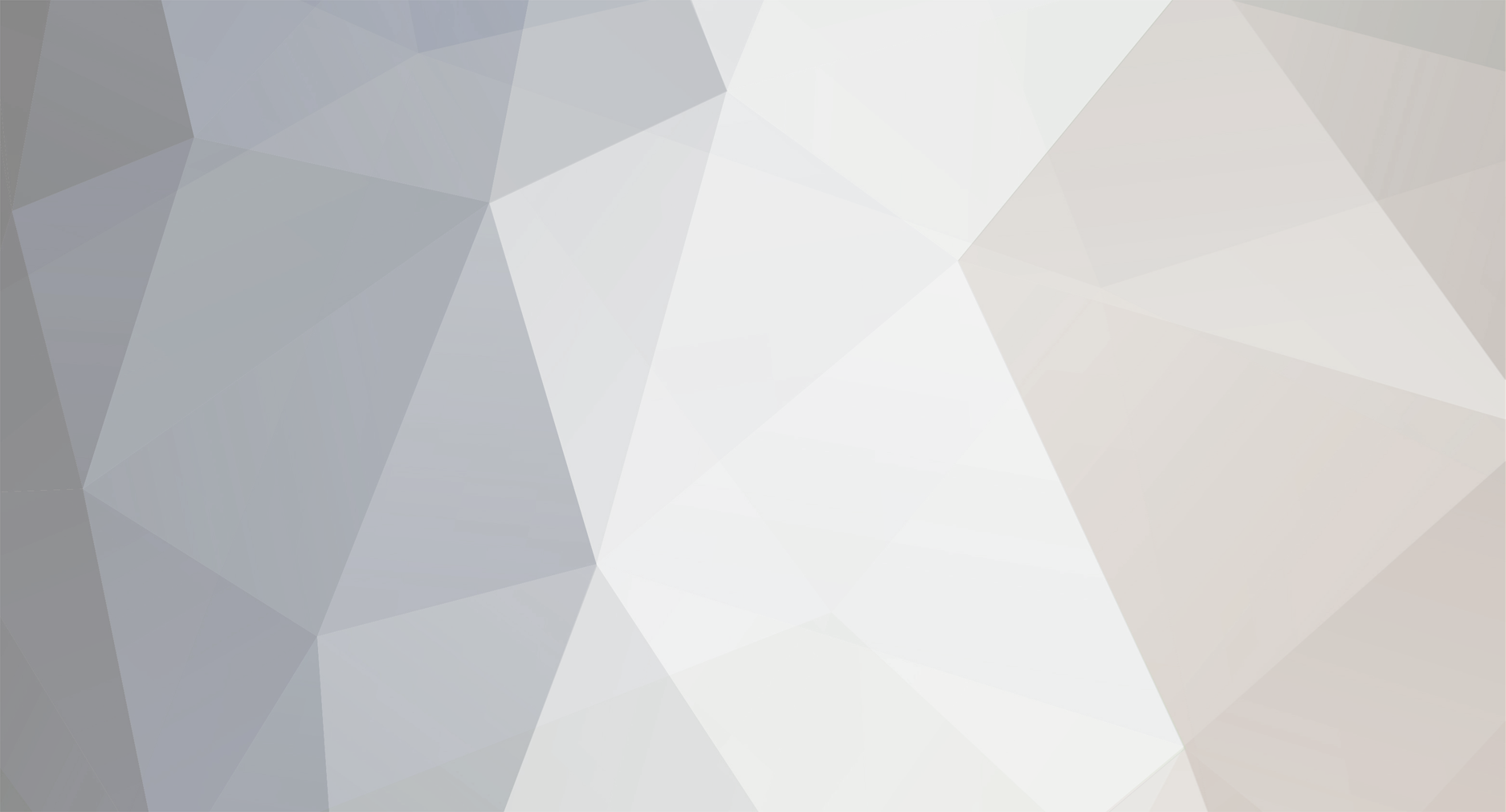
unclebill
Member-
Content Count
37 -
Joined
-
Last visited
Content Type
Profiles
Forums
Gallery
Blogs
Calendar
Store
Everything posted by unclebill
-
Saiga .308 Conversion to Pistol Grip Configuration
unclebill replied to turkmcl's topic in Saiga .308
ok here it is . it looks like crap but it wont move. i put black tape on it to make it black. i didnt feel like painting it.... tools needed i forgot the tinsnips -
i bit the bullet....(sorry).... and bought 2000 rnds. of lake city match ammo. i dont shoot my saiga like a madman so 1000 rnds. lasted me about a year.and of course i saved the brass. i also bought 1000 cleaned lake city match cases from a man on a forum like this $80 i use the cases until they start forming the shiny ring near the base. yes i get about 6 uses or so out of the brass. full length resizing will shorten the life of the brass.
-
unfortunately i have a bad back and am only able to shoot from a bench. that is why i no longer hunt. so i am a bipod guy.
-
Saiga .308 Conversion to Pistol Grip Configuration
unclebill replied to turkmcl's topic in Saiga .308
i had some sheet copper laying around so i wrapped some around the safety and crimped it into place. time; about 90 seconds -
fossten, hey no fair! you got a cooler p-grip than me! i would love to put a galil type front handguard on mine but i want to still use the bipod. any suggestions?
-
ok i wanna join in the fun too! here are the before and after it does feel better in my hands this way. i liked the original configuration too. aw hell i like saigas!
-
the 1st kind of rubber i tried didnt last very long at all. that car door stuff may be just the ticket!
-
Any chance of a pic for exact location? you bet! the lack of photos is what added about 10 hours to my conversion! i put blue tape on it so it is easily visible
-
Saiga .308 Conversion to Pistol Grip Configuration
unclebill replied to turkmcl's topic in Saiga .308
It isn't that bad to get the BHO in if you have a twist tie or string. Slide it in when you put your hammer in. Then place the spring inside with a twist tie or string around it and out through the bottom hole that the lever pops out. Then put when you slide in your trigger pin pull the string down so it can go through it and under the back half of the lever. Assemble the rest of the gun and bam you have a BHO built in. The only draw back to that vs the notch is that it can ding your finger when firing. The draw back to a notch is if the gun is jostled it will drop a -
the saiga creases them. i put a piece of rubber on the ejection port and the charging handle. that eliminated the brass damage. i have been thinking of trying that liquid rubber that is used on tool handles.
-
Saiga .308 Conversion to Pistol Grip Configuration
unclebill replied to turkmcl's topic in Saiga .308
thats a redfield wideview 3x9x40 scope i just had laying around. its about 30 years old. i cant remember how much it was.but i like this scope. i dont know if it will stay on this rifle. i have a couple more i may try out. -
Saiga .308 Conversion to Pistol Grip Configuration
unclebill replied to turkmcl's topic in Saiga .308
fossten, you my friend have made my day! for a while there i thought this was some kind of cruel hoax. i was getting ready to look it up under urban legends. -
Saiga .308 Conversion to Pistol Grip Configuration
unclebill replied to turkmcl's topic in Saiga .308
ok there is a forward facing hook and a rear facing hook. when i hold my trigger down and pull the bolt carrier back,the rear hook engages. when i let go of the trigger the hammer moves a little bit forward and is caught by the forward hook. is this the way it oughta be? please say yes! -
Saiga .308 Conversion to Pistol Grip Configuration
unclebill replied to turkmcl's topic in Saiga .308
i dont know if i will use it or not. it is kinda a pain . i think i will just cut a notch in the lever instead. -
Saiga .308 Conversion to Pistol Grip Configuration
unclebill replied to turkmcl's topic in Saiga .308
i think im done but what it this? and where does it go? i used the tapco pin retainer plate. -
Saiga .308 Conversion to Pistol Grip Configuration
unclebill replied to turkmcl's topic in Saiga .308
-
Saiga .308 Conversion to Pistol Grip Configuration
unclebill replied to turkmcl's topic in Saiga .308
a long time coming but thanks to you guys i waded through it! -
Saiga .308 Conversion to Pistol Grip Configuration
unclebill replied to turkmcl's topic in Saiga .308
yes! that is a GREAT idea!!!!! -
Saiga .308 Conversion to Pistol Grip Configuration
unclebill replied to turkmcl's topic in Saiga .308
You have better than a photo, you have a finished stock hammer to compare it to. What I did was put my cleaning rod through both hammers side by side so I could have them lined up and see the difference. I ground down the hump until it had just about a couple of millimeters left above the tube. Then I added a shallower angle to the whale's head to prevent the bolt from hanging up. I went slowly, grinding a little at a time and refitting, trial and error until I got the fit I wanted. Install the hammer after you grind a little and pull the trigger to see how it's doing. Then grind some mo -
Saiga .308 Conversion to Pistol Grip Configuration
unclebill replied to turkmcl's topic in Saiga .308
You have better than a photo, you have a finished stock hammer to compare it to. What I did was put my cleaning rod through both hammers side by side so I could have them lined up and see the difference. I ground down the hump until it had just about a couple of millimeters left above the tube. Then I added a shallower angle to the whale's head to prevent the bolt from hanging up. I went slowly, grinding a little at a time and refitting, trial and error until I got the fit I wanted. Install the hammer after you grind a little and pull the trigger to see how it's doing. Then grind some mo -
Saiga .308 Conversion to Pistol Grip Configuration
unclebill replied to turkmcl's topic in Saiga .308
I'm glad I picked up a black jack safety lever. Works like a charm and makes it easy to hold the bolt open and switch from safe to fire while only having to move my finger not my entire grip. thanks for the tips! does anyone have a photo of a ground hammer? -
Saiga .308 Conversion to Pistol Grip Configuration
unclebill replied to turkmcl's topic in Saiga .308
how do you hold the hammer in position while looking to see if the pin is lined up correctly while holding a punch while tapping the punch with a hammer? did every one else have somebody to either tap the pin in or hold the hammer in place? i am not trying to make this hard but i see no way for one pair of hands to do this. if i ever get this thing together i am NEVER taking it apart as long as i live. i feel like all 3 stooges rolled into one.. -
Saiga .308 Conversion to Pistol Grip Configuration
unclebill replied to turkmcl's topic in Saiga .308
Here ya go. http://www.cross-conn.com/Saiga_Conversion/Step_1.htm I would also like to add my experiences, although I'm not done yet. 1. I absolutely had to use the carbide dremel bit to cut the hole for not only the spot welds and the rivets, but also for the trigger guard hole by the PG nut hole. I also had to enlarge the PG nut hole. That steel is so tough my titanium drill bit barely made a dent in it. I decided that I couldn't drill the hole under the mag release, so I ground the paint off the TG and the surface directly under the mag release and used JB Weld, which works -
Saiga .308 Conversion to Pistol Grip Configuration
unclebill replied to turkmcl's topic in Saiga .308
Here ya go. http://www.cross-conn.com/Saiga_Conversion/Step_1.htm I would also like to add my experiences, although I'm not done yet. 1. I absolutely had to use the carbide dremel bit to cut the hole for not only the spot welds and the rivets, but also for the trigger guard hole by the PG nut hole. I also had to enlarge the PG nut hole. That steel is so tough my titanium drill bit barely made a dent in it. I decided that I couldn't drill the hole under the mag release, so I ground the paint off the TG and the surface directly under the mag release and used JB Weld, which works -
i have been searching this site for instructions on how to convert my .308 for a while now. i have FBMG 20 rnd. mags. maybe im stupid but i gave up after 1 1/2 hours and decided to start a thread. thank you for your time! bill that tutorial that i found online is wonderful BUT it doesnt help me with my .308 . i thought i could do it by following carefully NOPE!. THE .308 IS DIFFERENT THAN THE .223 AND THE 7.62X39. i have a bench covered with parts to prove it. i cannot find a .308 tutorial anywhere what a bummer.........